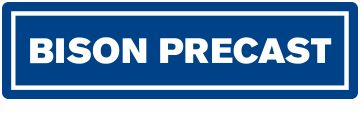
About
Everything we do is built around our customers.
Bison Precast is ready to meet your requirements, whatever your sector. From housebuilding and commercial to infrastructure and stadia, there’s never been a better time to build with Bison.
Our heritage
Founded in 1919 by two Royal Engineers who had created the pillboxes used on the Western Front in the First World War, Bison Precast has come a long way. Throughout our history, we have built innovation and passion into every component while delivering speed, strength and quality to the industry sectors we’ve come to know and understand. It’s a past we’re proud of and one which provides a solid foundation for our future.
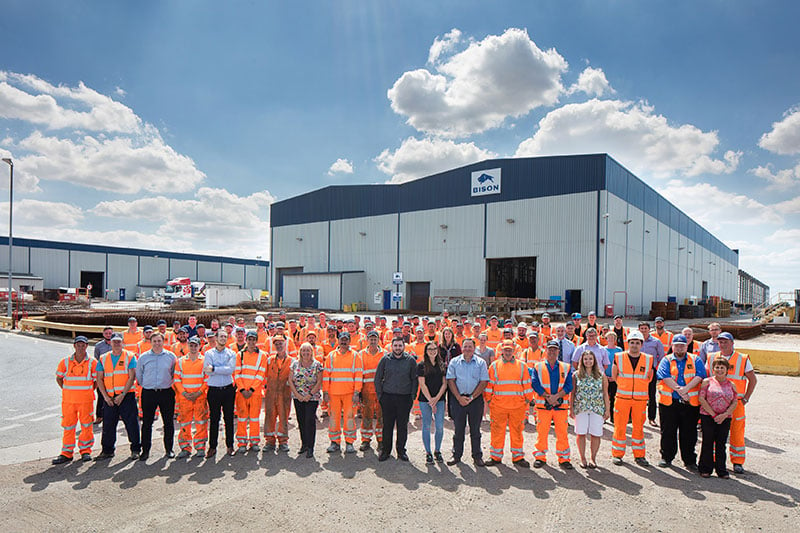
Bison today: a leader in offsite manufacturing
Today, Bison Precast is one of the most recognised names in construction. It is a leading UK manufacturer of concrete and is Britain’s largest producer of precast flooring. Its expertise and pioneering techniques are at the forefront of offsite construction, providing precast frame solutions that are reducing build times, improving health and safety, and helping alleviate issues of labour availability.

Innovative precast solutions to deliver your project
At Bison Precast, we understand the world you work in and so we develop the innovative, technically advanced solutions you need to deliver your projects. Our experience and technical expertise enable us to develop solutions for a wide portfolio of markets – from commercial, industrial, stadia and leisure to residential, car parks and infrastructure.
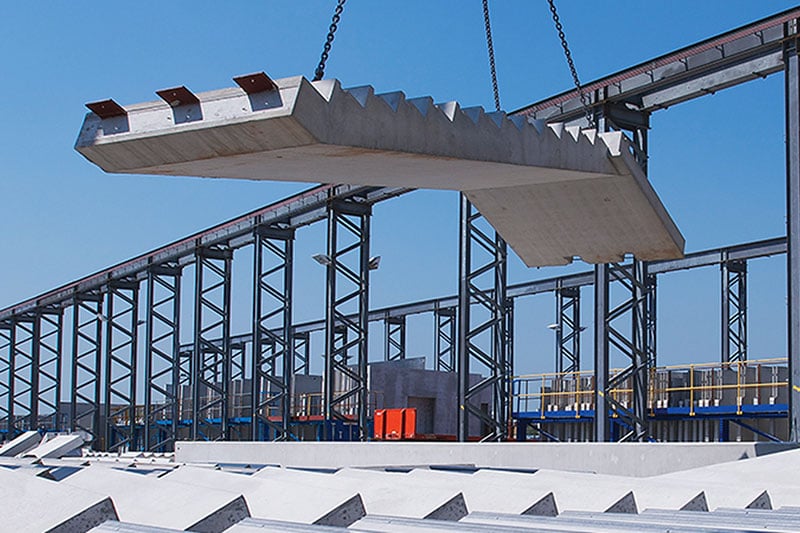
Tailor-made products manufactured off site
Whether you need flooring, structural precast, infrastructure or architectural products, our Design for Manufacture and Assembly (DfMA) approach ensures we are able to produce consistent, high quality precast concrete products and façades in factory-controlled conditions. Unhindered by weather or labour shortages, it means you are able to realise cheaper, faster and safer builds.
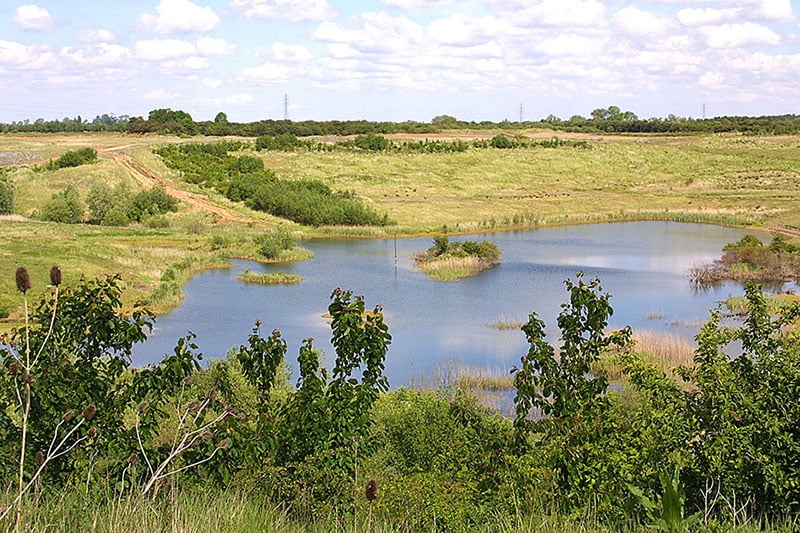
Sustainable and quality assured
Bison Precast products and façades are BES Responsible Sourcing Certified and are manufactured in accordance with ISO 14001 Environmental Management System. As well as being manufactured efficiently, they also have a long, low-maintenance service life. Our precast components are CE marked against BS EN 1168.
Bison Precast: projects delivered
Read how our products and people have helped to deliver technically advanced, innovative solutions for a range of demanding projects.
See more case studiesWe've got the precast concrete solutions for you
To help you in your decision-making process, our brochures contain useful information about the product ranges, their applications and technical specifications.
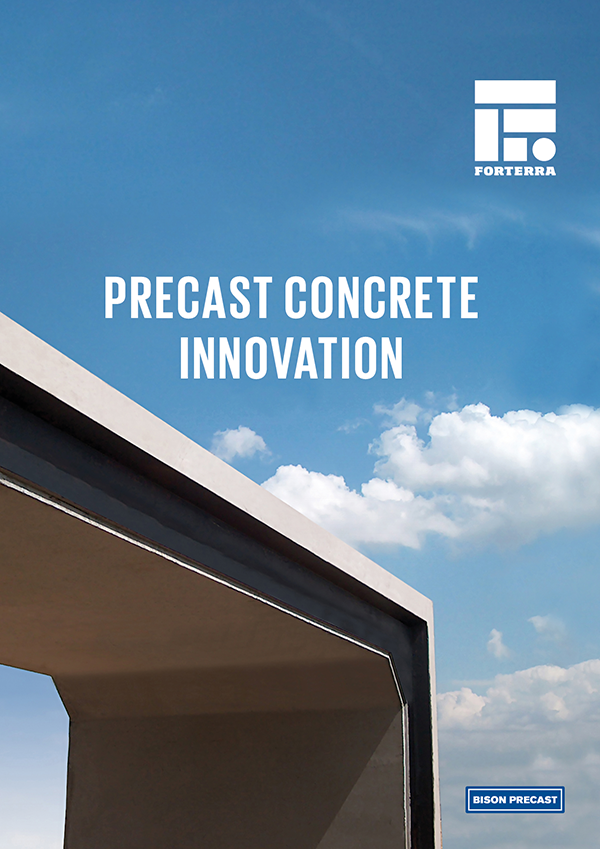
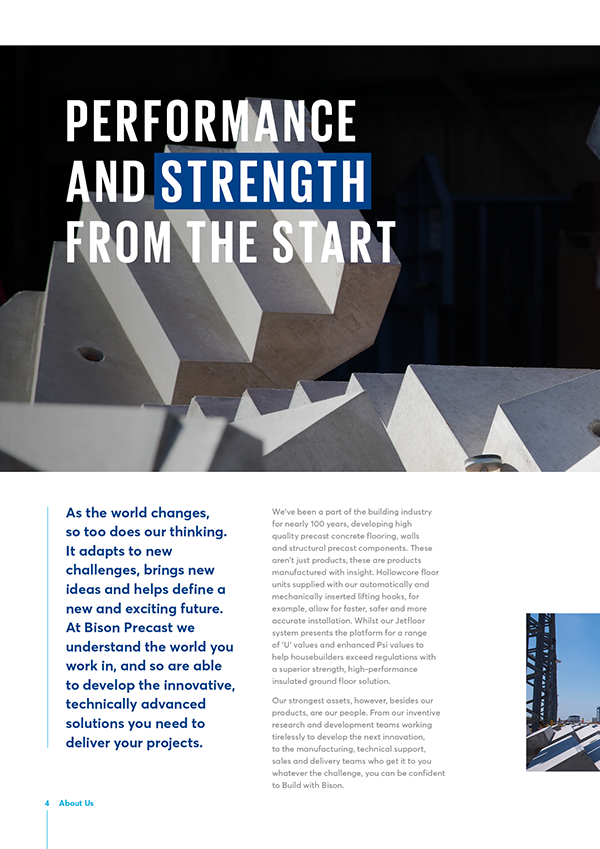